C2 PROJECT
C2 Project News
August 2025
The challenges of working to high precision - Part 2
The August working party continued where we left off in July.
Having learnt that the accuracy of our milling operation on the crosshead lower slipper was likely being influenced by flexing of the milling machine we had used, we had a decision to make. Should we 1) try to set up the slipper alone on a milling machine (very difficult to do, requiring shimming in all three planes) or should we 2) try to repeat the "milling in situ" operation using a chunkier milling machine. Andrew and Dave gave the matter some consideration and, after inspecting the machines available, decided on option 2). At least that might give us a better datum to work to if we then had to resort to option 1).
Once again, the Fireman's side piston and rod, the crosshead including lower slipper, and dummy little end bearing pin were assembled in the machine shop, but this time on the Archdale milling machine. The Archdale is a quirky machine, and Dave had only used it once before, but with some careful experimentation we discovered how to operate it.
This time we used just three V-blocks to support the workpiece, two under the dummy little end bearing pin and one under the outer end of the piston rod. This three point support arrangement was rather easier to set up than the four point support arrangement we had used previously. We started by using a height micrometer to try and get the top of the piston rod parallel to the table of the machine in the vertical plane. Then we used a dial test indicator to get the side of the rod aligned in the horizontal plane. A final check of the top of the rod using the dial test indicator showed a small error in the vertical plane, so additional shims were added to correct it and the whole process repeated.
With everything finally clamped down, we centred the milling cutter over the previously machined slot by eye (accurate enough when there is still several millimetres of material each side), and took a 10 thou deep cut. There was no chatter from the cutter (the same one we used last time) which was a good sign. Time to again check the parallelism of the cut and the piston rod.
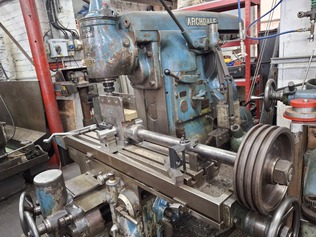
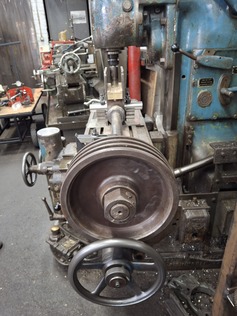
Crosshead and piston set up again on the Archdale milling machine.
Because the engineer's parallel we have is too long to fit when the cutter is aligned with the slot, the workpiece had to be moved sideways each time we wanted to carry out some measurements. With no digital readout on the Archdale, this meant we lost our lateral datum each time; frustrating but we eventually got pretty adept at lining the cutter up by eye.
With the engineer's parallel in the slot in the slipper, we used an internal micrometer to take a couple of readings along the piston rod. Over the 500mm length of the rod, we still had 8 thou of error. At this point we almost decided to abandon milling the slipper in situ and go for option 1), but Andrew made a good suggestion. Why not take another cut of the slipper, measure again, and find out how repeatable the error is? So that is what we did.
After the second cut, the error in parallelism was still 8 thou over 500mm. Very repeatable! The little end bearing pin on its V-block supports is about 200mm away from the measuring points, so a little trigonometry suggested we needed to remove 11 thou from under the little end bearing pin. Doing so involved unclamping the workpiece, so the whole process of setting up the lateral alignment had to be gone through again. Since we had deliberately set the shims to try and correct the alignment in the vertical plane, we didn't need to clock the piston rod in the vertical plane, but we did so just out of curiosity. This suggested an 8 thou error over 500mm, though we expected that given that we'd taken some of the shims out. At least we were still getting consistent values.
With the workpiece clamped down again, and with the cutter centred reasonably on the slot in the slipper, yet another 10 thou cut was made. With the cut taken, the cutter was moved out of alignment so that the engineer's parallel could be put in place again. A couple of sets of measurements were taken along the piston rod to determine how parallel it was to the engineer's parallel (and hence the slot in the slipper). The measurements came out exactly the same! At last we had made a cut that we were confident was in exactly the correct plane.
All the setting up, taking a cut, measuring, adjusting, re-setting up, and so on is not a quick process, and the above described exercise took us all of Saturday and into Sunday.
Next stage was to line the cutter up accurately with the lateral centreline of the piston rod. Erle was working at Dinas on the NG15 again this weekend, but very kindly offered to drop his edge-finder off with us on Saturday evening. This meant that, on Sunday, Andrew and Dave were able to use it to line up the head of the milling machine, firstly over the edge of the piston rod, and then (after measuring the diameters of the piston rod and edge-finder) over the centreline of the rod. The edge-finder was replaced in the head of the milling machine by the cutter, and we were ready to start deepening the slot in the slipper.
We decided to leave a little material in the bottom of the slot, as it will need a final machining operation after we have white metalled it. Having already cut a slot about about 5 millimetres deep during our experimentation, we had another 12.5mm of material to remove. Taking 1mm deep cuts, Andrew used the Archdale to chomp through the brass.
While Andrew was removing material, Dave went back to the C2 shed to do some calculations. Andrew had previously prepared a drawing showing the relative positions and exact dimensions of the piston rods and slidebars. The crosshead slippers have to fit around the slidebars with a small clearance. Dave therefore calculated exactly how wide the slot needed to be to provide the necessary clearance. On the Fireman's side, the slidebar is centred perfectly over the piston rod, so the slot will be centred on it too. However, on the Driver's side there is a small deliberate offset to compensate for alignment errors in the motion bracket and cylinder castings, so this needed to be accounted for.
Back in the machine shop Andrew had completed deepening the slot in the slipper. To ensure that we got the slot exactly the correct width, rather than rely on the graduations on the machine, we used a dial test indicator to monitor the lateral position of the table. Andrew started with a 1mm deep cut, increasing the width of the slot by 2mm. The machine made such little fuss about it that we rapidly increased the depth of each cut to 2mm, and the width to 3mm and then the final 3.96mm.
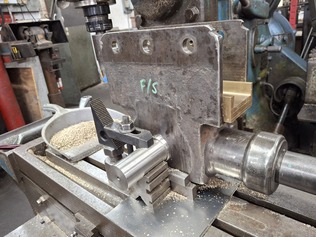
The channel in the crosshead slipper machined to fit the slidebar.
After completing the cuts to form one side of the slot, Andrew measured the width of the slot to confirm that it was exactly the width of the cutter (50.25mm) plus 3.96mm. It was. The surface finish on the side of the slot was also excellent, thereby confirming that the problem we'd had before with the cutter chattering was due to the milling machine we had used and not the cutter. Andrew therefore moved the table across to widen the slot by 3.96mm on the other side.
By this time it was Monday, and the works' staff were on hand to advise us when the next problem arose. A final check, to confirm that the bottom of the slot in the slipper was still parallel to the piston rod involved placing the engineer's parallel back into the slot. But because the slot was deeper and it's bottom (and hence the engineer's parallel) was closer to the piston rod, we could no longer get the 2-3″ internal micrometer we had used previously in the gap. Merik offered us the use of his 1-2″ internal micrometer which did fit, but Keith also suggested we use slip blocks.
Slip blocks are small, incredibly accurately ground blocks of metal. Although the thinnest block was about 40 thou, some of the increments in the set are considerably less than a thou, so, by selecting combinations of them, a huge variety of very precise thicknesses can be obtained. Neither Andrew or Dave had used slip blocks before, so that was another skill learned! Fortunately, both the slip blocks and Merik's internal micrometer gave exactly the same readings, and more importantly, showed that the bottom of the slot in the slipper was still parallel to the piston rod (within no more than 0.5 thou).
For the moment, we now have the Firemen's side lower crosshead slipper milled out to the correct width and almost to the correct depth. We will mill a recess into the bottom of the slot and fill it with white metal before finally cutting the slot to full depth. Importantly, we have had a lot of practice at setting up and measuring the crosshead/piston rod/piston assembly, and have developed a method for forming the slot in the slipper. Machining the Driver's side slipper will thus (hopefully!) be a lot quicker. We're quite looking forward to having a go at that one.
During a break in the above proceedings, Andrew used a gas set to heat up the stainless steel reverser intermediate crank pivot sleeve and to drop it over the pivot pin. After the assembly had cooled, and while Andrew was widening the slot in the crosshead slipper, Dave polished the pivot sleeve. The reverser intermediate crank is fitted with a plastic bush which interfaces with the stainless steel sleeve. Although the sleeve goes part way into the bush, Dave found that it was then jamming. After some careful measurement, it seems as though the hole in the reverser intermediate crank that the plastic bush was pushed into wasn't round. Either the inside of the bush will need to be skimmed on a lathe, or the bush pushed out and the hole re-machined.
Andy joined us for the day on Sunday. He had previously cleaned up all the components of the piston rod glands, so Dave tasked him with measuring the components and sketching them so that they could be drawn up as a homework project. The piston rod glands are of an unusual design, and are very different to the original design for which we have drawings, hence the need for a new set of drawings. Furthermore, we need to understand how the components of the piston rod glands fit together. For example, there are three packing rings, which is odd because the C2 only has two cylinders!
Andy spent a quiet day sat in the C2 shed with a pen and paper, measuring equipment and the piston rod gland components laid out in front of him. By the end of the day he had measured and drawn them all, and had solved the conundrum! The gland housings on the two cylinder covers have been machined differently. By selecting the correct combinations of components, and putting two packing rings in one side and one on the other, the sets of components have the same equivalent length.
Dave has discovered that the C2 piston rod gland design is very similar to the valve stem gland design used on rebuilt Bulleid Merchant Navy locomotives. The chief difference seems to be that on the Merchant Navy's there was a spring which kept the assembly in compression, whereas we didn't find any such springs when we took the C2 piston rod glands apart. Andy's measurements and calculations indicate that the C2 relies on the nuts holding the gland covers on applying some compression to the gland internal components. This doesn't seem ideal, as it would be easy to over-compress the glands, and they will slacken as they wear. But it must be a design which worked reasonably well in China, so we'll give it a go.
After the frustrations of the previous working party, this one was a real success. We've found a way of machining the crosshead lower slippers to the accuracy we desire, which at one point was looking impossible. That's very satisfying. And we now have a good understanding of the piston rod glands too. Real progress!
Checking if the fireman's side cross head slipper fits the slidebar
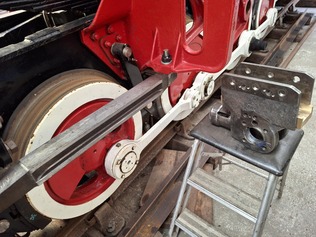