C2 PROJECT
C2 Project News
Easter 2024
Easter weekend 2024
The weekend before the Easter working party, Chris was in Porthmadog and kindly offered to carry out some work on the C2 for us. On the Friday he completed reaming the holes in the draincock reach rod and associated crank. With fewer people around over the weekend he restricted himself to only working on "safe" activities, i.e. those not involving power tools and machinery. But that didn't stop him carrying out some very useful tasks. Paint was applied to the draincock linkage parts, to prevent them corroding. The the works' staff were consulted, and the draincocks were measured to enable us to specify gaskets for them. Chris also measured some of the boiler components, so that Dave 1 could draw them up at home.
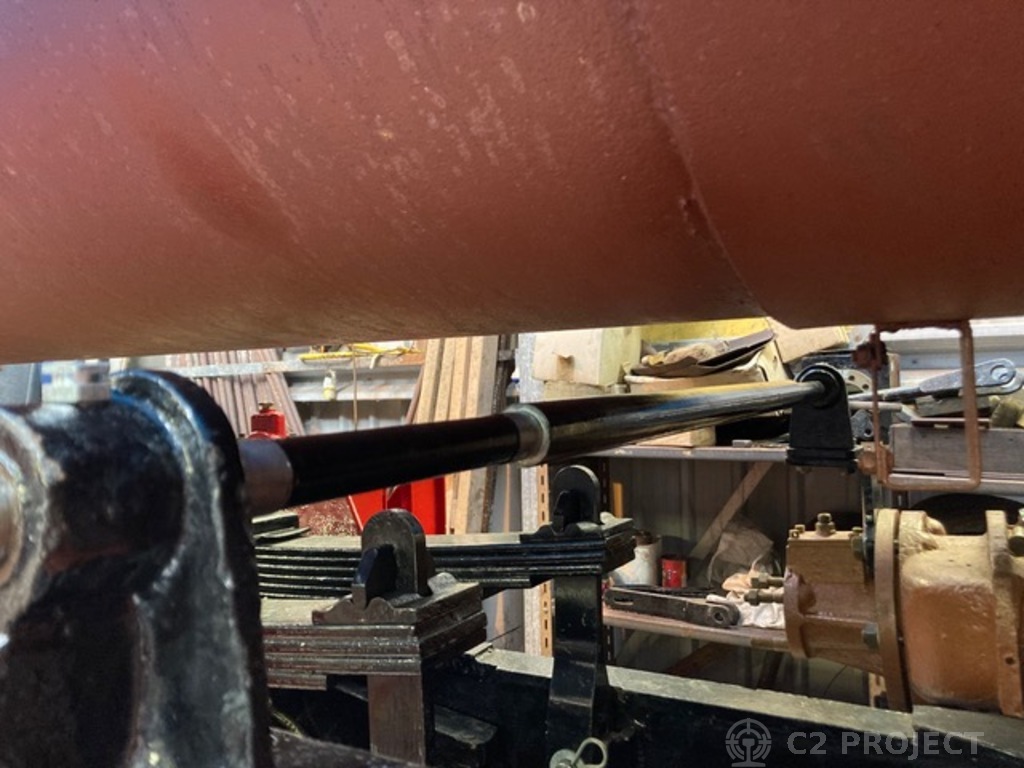
Chris has painted the draincock weighshaft.
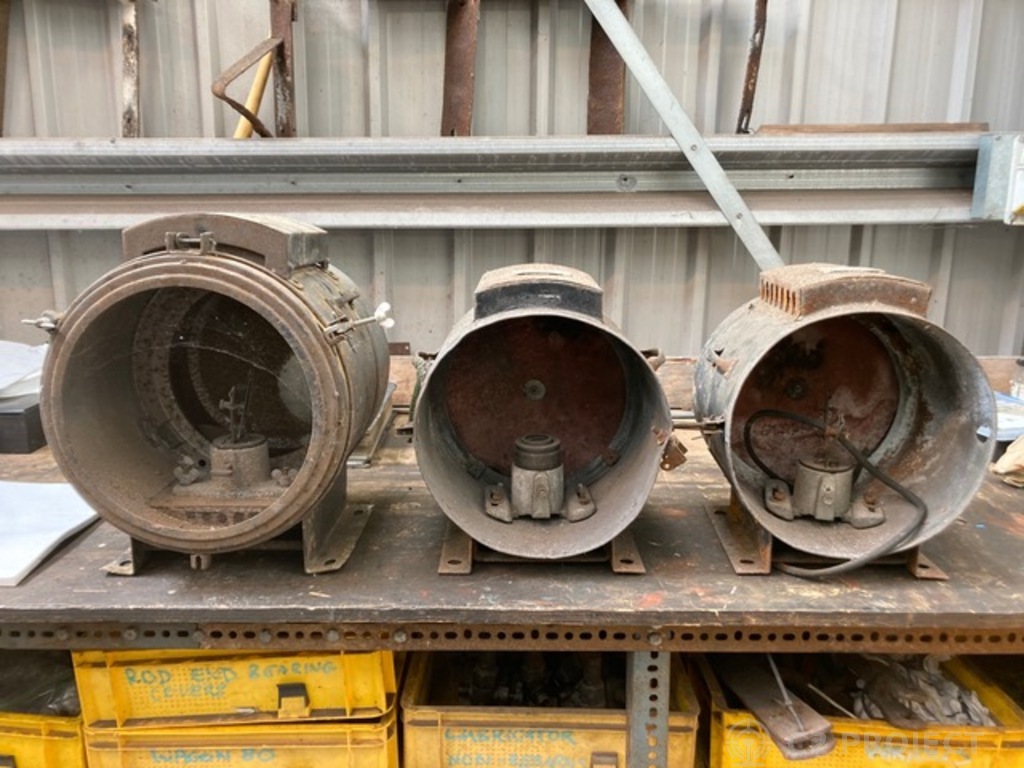
Chris has been measuring up the mounting brackets for the loco head and tail lamps.
The Easter working party itself was dominated by machining tasks.
Dave 1 started by turned up a couple of spacers for the grease nipples fitted to the draincock lower weighshaft bearings. Whilst only small parts, once fitted they allow the grease nipples to be screwed into place without locking the weighshafts which pass through the bearings.
Next Dave 1 turned his attention to the pins which hold the draincock lower links to the associated cranks and operating rods. These are made from mild steel, only seeing small, infrequent movements. There are four of them though, and the diameters needed to be fairly precise. Dave soon got a production system going, and all four pins were turned.
Across the machine shop on another lathe, James was given the task of machining the pins for the draincock droppers and reach rod. These are a little bigger than the pins Dave 1 was making, and, being fitted into plastic bushed holes, are made from stainless steel. James soon got into his stride, and was turning out pins to a precise diameter and with a good surface finish. We only need five of these pins at this stage (four for the droppers and one for the return rod crank) but James was enjoying himself so much he ended up making six pins! The spare won't go to waste, since, at some stage in the future, we'll need it at the cab end of the reach rod.
While the lathe was set up, Dave 1 also turned up a couple of stainless steel collars for the return rod/expansion link joints. The pins for these will need to be made at a future working party.
Dave 2 was tasked with drilling all the pins to accept split pins. The upper weighshaft also needs similar holes to prevent the cranks from sliding axially on the shaft (rotation is prevented by keys in keyways). Drilling a diametric hole through a pin (especially one made of stainless steel, which isn't the easiest material to work with) is challenging, but Dave is quite an expert at it now.
The plastic bushes which we ordered at the previous working party had arrived, so Dave 2 fitted them into the appropriate holes in the draincock droppers and cranks. With most parts now complete, Dave was able to assemble much of the draincock linkage mechanism to check that it works. Needless to say, it does! There is no discernible play, but the mechanism moves very freely. This just leaves the draincocks to be fitted and the operating rods to be finished.
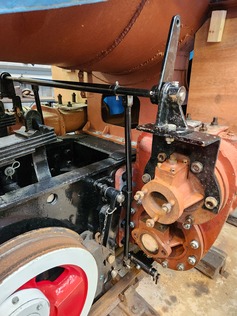
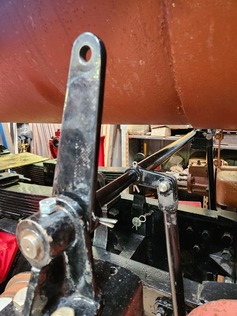
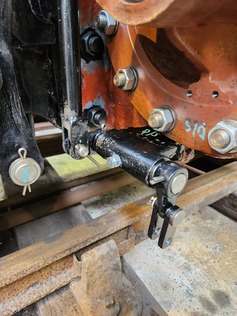
Drain cock linkage assembly trial fitted by Dave 2 with the new pins as made by Dave 1 and James
Andrew chose to undertake the most challenging task of the weekend. As previously reported, the expansion link trunnions are at some very strange angles relative to the expansion link itself. Although the expansion links do not rotate through large angles, if the trunnions are not perpendicular to the links they will cause considerable wear (and hence slack) in the bearings. But how to resolve this?
The new expansion links have not yet been delivered, but they are essentially flat plates with a curved slot in. The side plates which carry the trunnions mount onto the expansion links with four bosses. Andrew found that the four bosses on each side plate are not co-planar as they should be. Although the bosses will pull into place when bolted up to the expansion link itself, this will result in movement of the trunnions, which means we have no reliable datums to work to.
Dismantling the first expansion link assembly, Andrew found that one side plate was more distorted than the other. The most distorted plate was clamped to a flat surface and heated to relax some of the internal stresses. This helped to straighten it out a little.
The other side plate was not so bad. James quickly turned up a bush to fit into the return rod/expansion link joint hole, which could then be used as a datum. By careful measurement, Andrew found that the trunnion on this side was not far off perpendicular to the mean plane of the bosses, although the distance between the centre of the trunnion and the centre of the return rod/expansion link joint was about 0.5 millimetre out of tolerance.
Andrew figured that the bosses could be brought into a flat plane by skimming them on a milling machine, using the 'good' trunnion as a datum. Only a fraction of a millimetre of material needed to be removed before all four bosses were co-planar.
Fortunately the current holes for the return rod/expansion link joints are under size (we will be enlarging them to take bushes) so there is metal available to move the hole in order to bring the distance between the centre of the trunnion and the centre of the return rod/expansion link joint back into tolerance. Andrew used the CNC milling machine to align the new hole centre precisely, and then used a boring head in the milling machine to re-bore the hole in the correct place.
The second side plate could then be bolted to the first, and a reamer re-run through the fixing holes to ensure they are all perfectly aligned. The assembly was then re-mounted on the milling machine, and the second return rod/expansion link joint hole bored to be in line with the first.
We now knew that the 'good' trunnion on the first side plate was perpendicular to the plane of the expansion link, so this could be used as a datum for measuring the other trunnion. To do this, Andrew removed the bed extension of one of the 17 inch DSG lathes, and held the 'good' trunnion in a three jaw chuck. The opposite trunnion is up to 2 millimetres out of alignment, but it will be fitted with a stainless steel sleeve which is thicker than this. Our plan is therefore to fit one of the existing (newly made to the correct diameter) stainless steel sleeves to the 'good' trunnion and to make an oversize sleeve to fit on the opposite one. This can then be turned down in situ, knowing that it is co-axial with the 'good' trunnion.
Andrew expressed some frustration that the process had taken almost four days, and that we still have another expansion link assembly to sort out. However, it was pointed out to him that he had devised a process for measuring and correcting what appeared, at the outset, to be an impossibly complex problem. It is likely, therefore, that the corrections required for the second expansion link assembly will take far less time and will certainly be a lot less daunting.
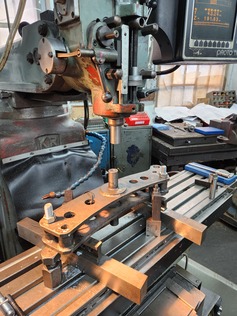
Andrew re-machining the expansion link face plates.
All the time that the above tasks were taking place, Erle was at the back of the erecting shop, using the Wanderer milling machine to chomp through the block of steel he is using the make a new reverser base plate. At the start of the working party, it was a two man job to lift the block of steel, but by the end it is now liftable by one person and is beginning to look like the final component. Erle has started to machine some of the more complex shapes into the back of the plate, so it is no longer a case of waiting for the machine to do a complete run from end to end of the component. This will become increasingly the case as the base plate takes shape.
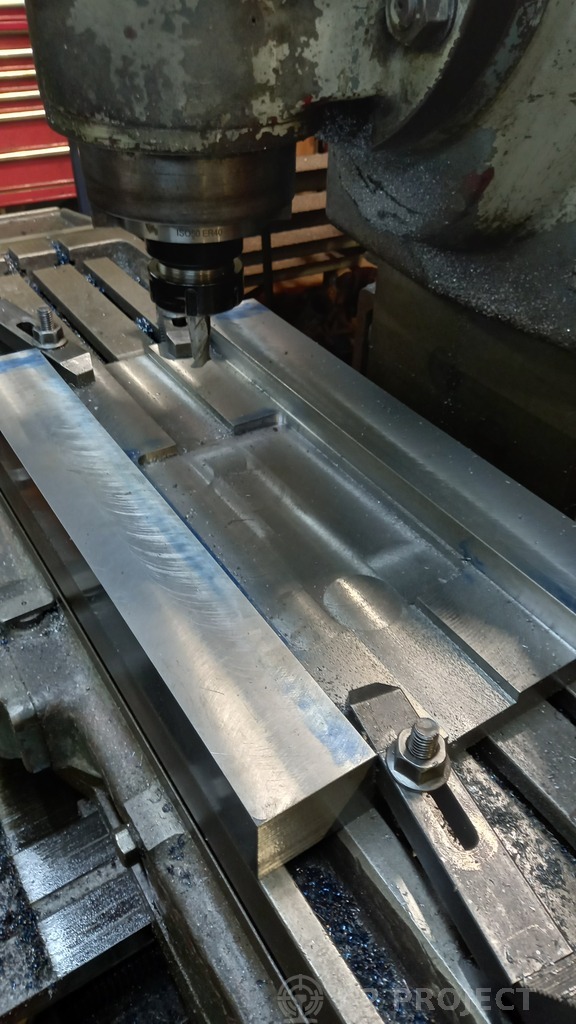
Erle continues to machine the new screw reverser bracket.
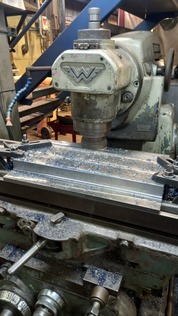
The basic shape of the screw reverser bracket is now becoming obvious.
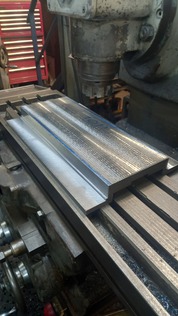
As well as working on the C2, Andrew was Duty Site Supervisor on Saturday, which involved trying to diagnose a brake fault on Blanche, between trains. Andrew also volunteered to come into the works early on Sunday (even after we'd lost an hour in bed due to the clocks going forward) to help Robco resolve another problem on one of the Garratts required for service.
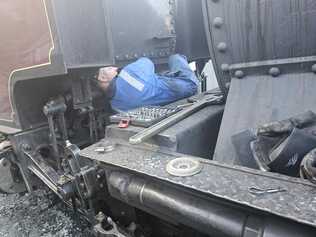
Andrew helping Rob fix Garratt (NG/G16) number 130 on shed at Boston Lodge on Easter Sunday morning before it pulls the train from Porthmadog to Caernarfon. (Photo - Tim O'Donnell)
In summary, we completed a lot of tasks which we had set ourselves for the working party. This means that the draincock linkages are now nearly complete, and we are starting to work on the motion. And, most importantly, we had a lot of fun!