C2 PROJECT
C2 Photo Album
album:Late June 2019
The tender chassis with crashbeam temporarily attached. Andrew tack-welded this together while bolted to the frame, and then completed the fabrication on the bench.The tender crashbeam temporarily assembled onto the rear bufferbeam. After studying numerous photos in our archive, we have concluded that the crashbeams and brackets were painted black by Harbin Works, and that is what we plan to do. Other works and railways sometimes painted them red.
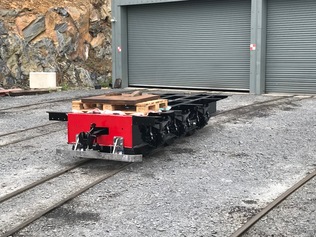
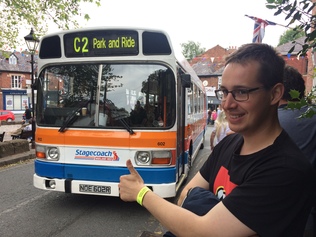
That's not a C2! Dating from 1976, this bus is a few years older than our loco. Spotted at the Lymm Historic Transport Day a week before our working party. William seems to approve...
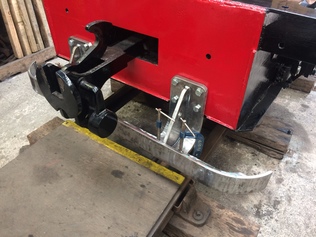
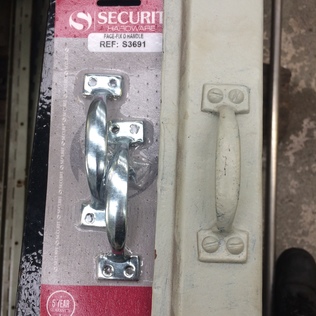
The cab window refurbishment required some additional handles, to replace originals that were missing or damaged. We found these in a hardware store, and they appear identical to the one surviving good handle. The packet says 'Proudly packaged in England' but I bet they were made in China!
The second motion bracket on the horizontal borer, set up for boring the hole where the slidebar is attached.
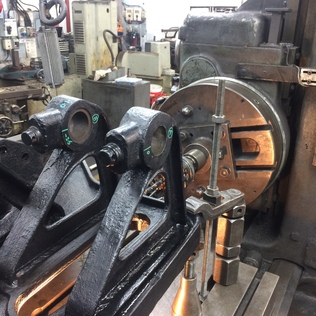
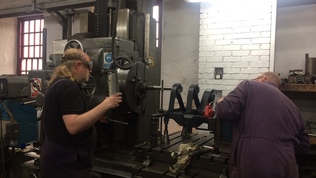
With the table rotated, the two Daves align the boring head to machine the expansion link pivots.
Alan is on the nearer lathe, machining a bush to guide a reamer in the expansion link pivot hole. Dan is in the distance, making dowels to align the slidebar and motion bracket joint.
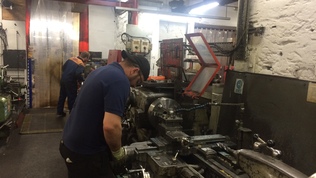
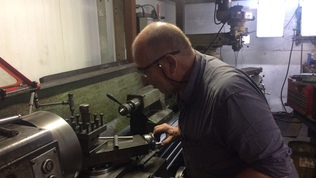
Colin on the big Colchester lathe, making parts for the brake gear pins.
In the welding bay, Andrew has completed the fabrication of the main crash beam and brackets, and is trial-fitting one of the footsteps.
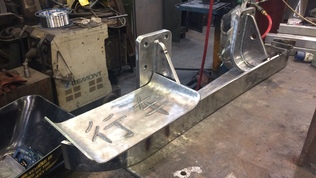
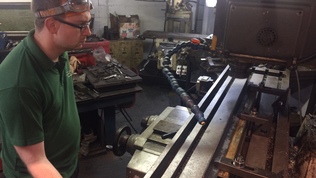
James has set up some steel T-section on the Bridgeport milling machine, to reduce its size slightly. These lengths will form part of the new cab door droplight window.
Alan and Andy use a large adjustable reamer to finish the bore in the motion bracket. This tool was kindly provided by CMS-Cepcor who assembled our wheelsets, and it has proved useful for a number of awkward tasks.
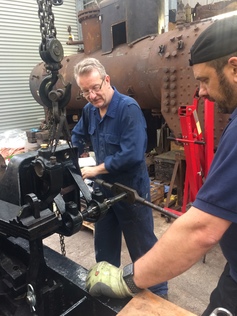
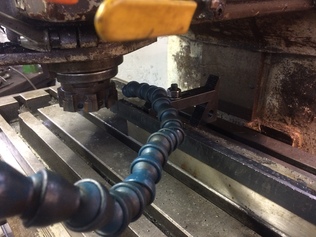
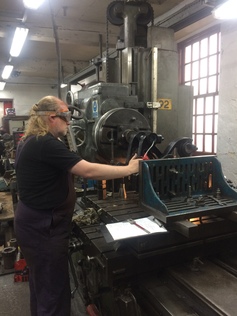
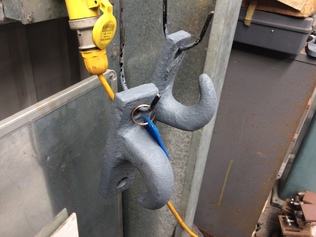
Cab lifting hooks, cleaned up by Arthur under Caleb's supervision.
The two lengths of hollow section prepared by Caleb and two lengths of tee machined by James that will form the basis of a new cab window droplight. We will also graft in some new pieces to the existing droplight (behind) to renew damaged areas.
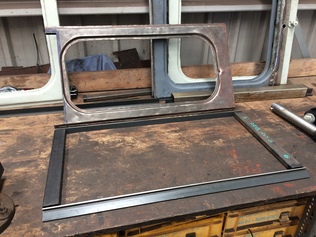
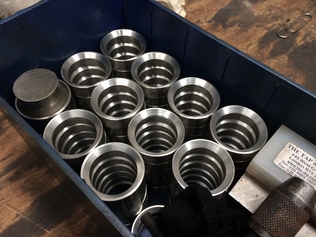
A box full of heads for brake gear pins, which kept Colin busy for much of the weekend.
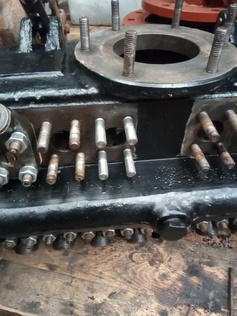
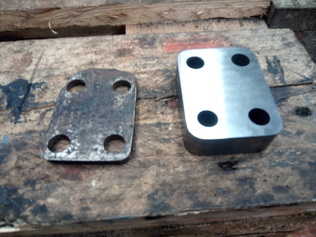
Lubricator blanking plates, old and new. Erle has done a lovely job of machining these. Making them the same thickness as the pump bodies means we can use standardised fastenings.
One of the lubricators with 10 pump bodies fitted.
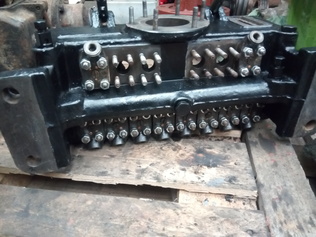
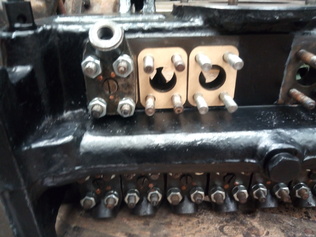
Erle has designed and bought a batch of gaskets for the lubricators, including some spares for the future. These two await the fitting of the blanking plates that go in these locations.
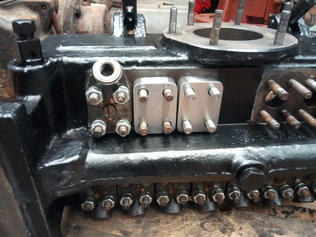
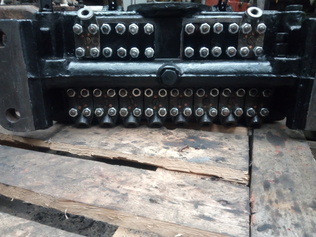
The underside of a lubricator with all the pumps and blanking plates fitted.
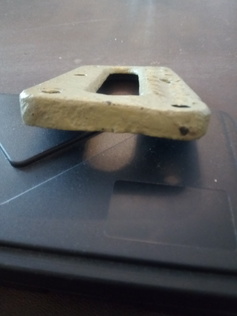
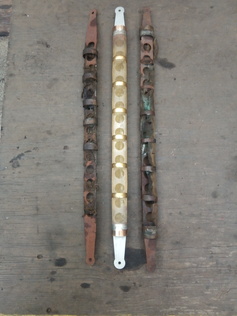
At the bottom of the lubricator vessel is a fine filter to prevent grit getting into the pumps. This was a complex assembly and the old ones were in a terrible state. Erle has done a beautiful job creating their replacements.
The filter, being trial-fitted into its location in the lubricator body. There is another hole below it, which takes the steam heating pipe.
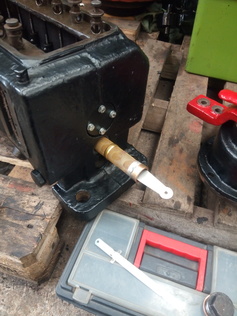
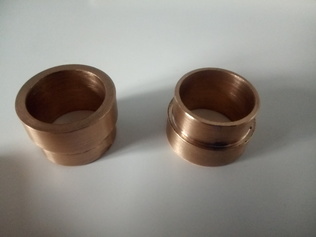
New brass ferrules which form the ends of the oil filter.
The lubricators have sight-glasses to show the oil level. One of the bezels that retain these glasses was rather bent, and the others were a bit rough. Erle has remachined them and is procuring rubber seals that will fit well against the glass.
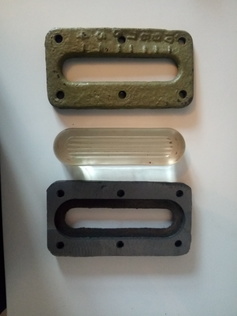