C2 PROJECT
C2 Photo Album
album:July 2022
Paul's grinding setup, with circular blanking plate, sealing putty, masking tape and a clamp to prevent any swarf getting into the bearings. The air-powered die grinder enabled a smaller groove to be made, with less heat input.
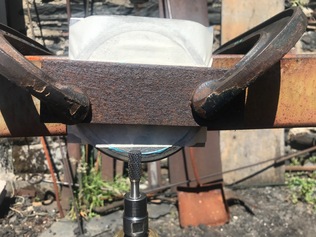
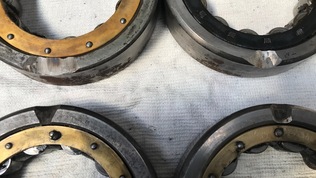
Close-up of the lubricant channels crudely ground in the leading end roller bearing races. This was probably done at Dahuichang; there is evidence of excessive heat and far more material has been removed than was really necessary.
A variety of six coupling rod roller bearings, all nominally the same but differing in detail. The four on the left came off the loco; bottom right was acquired unused from the stores at Dahuichang. Top right is one of the brand-new ones we have purchased.
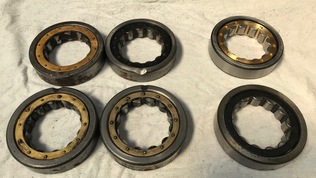
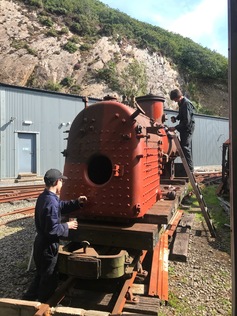
Gwion and Jack painting the areas they had cleaned up.
Jack decided to tackle the boiler barrel and made good progress along one side.
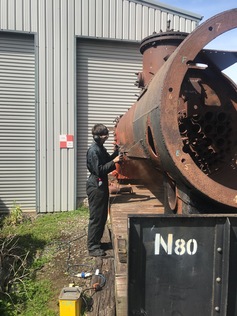
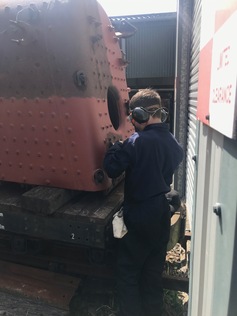
Gwion using a wire wheel to remove rust from the backhead.
First aid kit now installed in the C2 shed. We've always had fire extinguishers but this is another wise precaution.
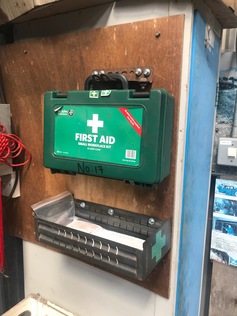
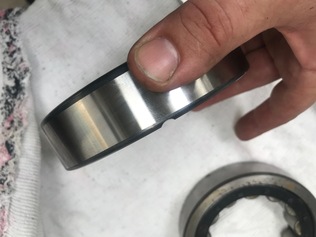
Completed lubricant groove - radial view.
Completed lubricant groove - axial view.
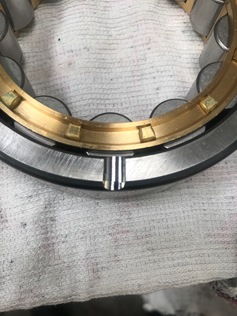
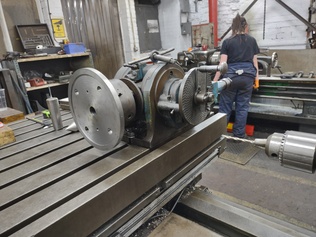
Turbine disc set up in the dividing head on the horizontal borer.
110 equally-spaced holes around the circumference of the turbine disc. Thanks Martin!
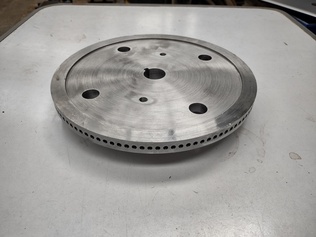
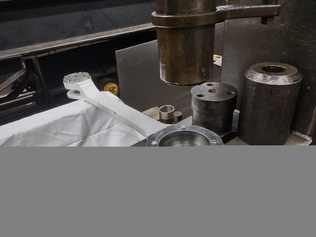
Axle 3 large bearing ready for pressing.
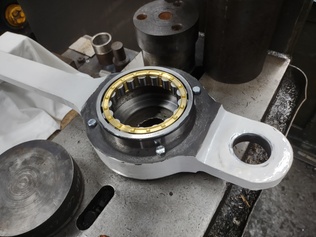
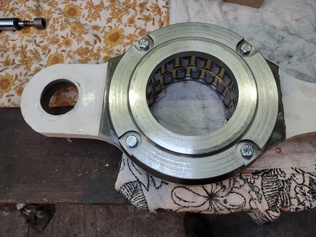
Completed assembly for axle 3 bearings.
Axle 1 small bearing ready for pressing.
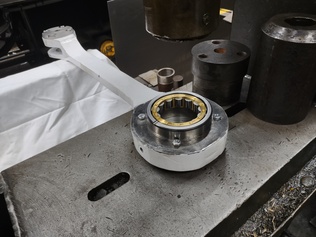
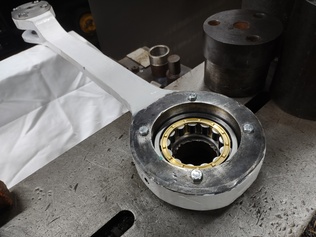
First bearing in position, ready for fitting the second one.
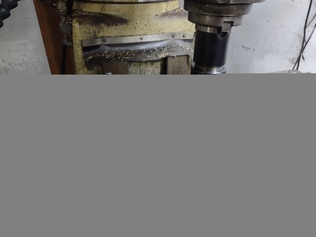
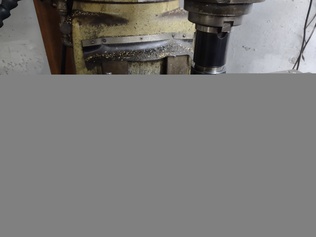
Final machining on the last bearing cover.
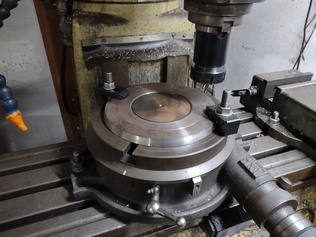
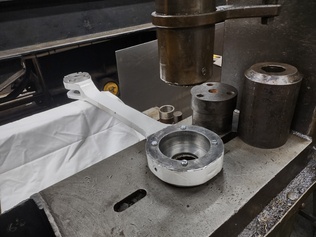
Preparation for pressing in the bearings.